Why plastic extrusion is the best choice for mass production
Why plastic extrusion is the best choice for mass production
Blog Article
A Comprehensive Overview to the Process and Benefits of Plastic Extrusion
In the huge realm of manufacturing, plastic extrusion arises as a highly efficient and vital process. Translating raw plastic into continual accounts, it provides to a variety of markets with its amazing convenience.
Recognizing the Essentials of Plastic Extrusion
While it might show up facility at very first glance, the procedure of plastic extrusion is basically straightforward - plastic extrusion. It is a high-volume production method in which raw plastic is thawed and formed into a continuous account. The process begins with the feeding of plastic material, in the type of powders, granules, or pellets, into a heated barrel. The plastic is after that thawed utilizing a mix of heat and shear, applied by a rotating screw. When the molten plastic reaches completion of the barrel, it is required through a small opening called a die, shaping it right into a desired type. The shaped plastic is then cooled down, solidified, and reduced into desired sizes, finishing the procedure.
The Technical Refine of Plastic Extrusion Explained
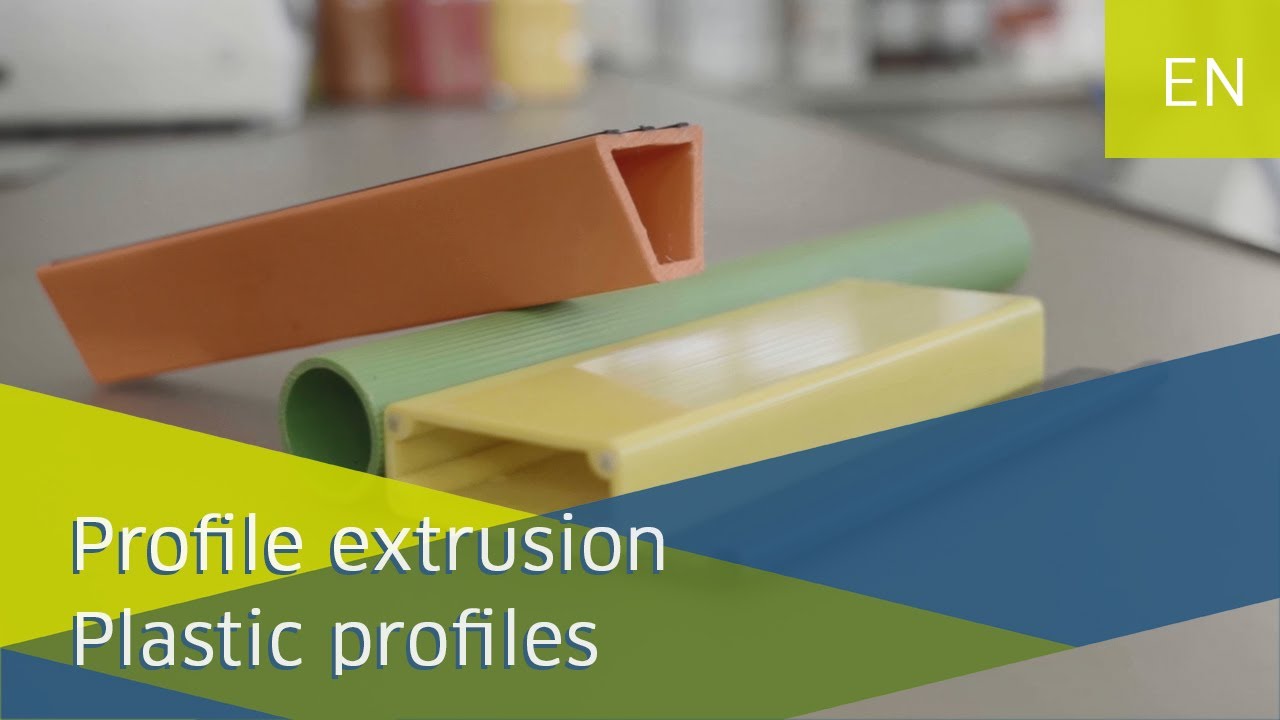
Sorts Of Plastic Suitable for Extrusion
The selection of the right kind of plastic is an important aspect of the extrusion process. Various plastics offer special homes, making them a lot more fit to specific applications. Comprehending these plastic types can substantially improve the extrusion procedure.
Contrasting Plastic Extrusion to Various Other Plastic Forming Techniques
Understanding the kinds of plastic appropriate for extrusion leads the way for a wider discussion on just how plastic extrusion compares to various other plastic creating methods. These consist of shot molding, strike molding, and thermoforming. Each technique has its special uses and advantages. Injection molding, for circumstances, is superb for developing detailed parts, while blow molding is perfect for hollow objects like containers. Thermoforming excels at developing superficial or big components. Plastic extrusion is unparalleled when it comes to creating continual profiles, such as seals, gaskets, and pipes. It also permits for a consistent cross-section along the size of the product. Hence, the option of method greatly depends upon the end-product requirements and specifications.
Key Benefits of Plastic Extrusion in Manufacturing
In the realm of manufacturing, plastic extrusion offers lots of significant benefits. One significant benefit is the cost-effectiveness of the process, which makes it a financially attractive manufacturing method. Furthermore, this technique supplies premium product flexibility and enhanced production rate, consequently raising general production effectiveness.
Economical Manufacturing Method
Plastic extrusion leaps to the forefront as an economical manufacturing approach in production. This procedure sticks out for its capacity site to produce high volumes of product swiftly and effectively, offering manufacturers with substantial cost savings. The key expense advantage is the capacity to utilize much less expensive basic materials. Extrusion utilizes thermoplastic products, which are much less pricey contrasted to ceramics or metals. Further, the extrusion procedure itself is fairly simple, lowering labor expenses. In addition, plastic extrusion needs much less energy than traditional production methods, adding to lower functional expenses. The process also lessens waste, as any type of faulty or excess products can pop over to this web-site be recycled and reused, giving another layer of cost-effectiveness. On the whole, the economic benefits make plastic extrusion a very attractive alternative in the manufacturing sector.
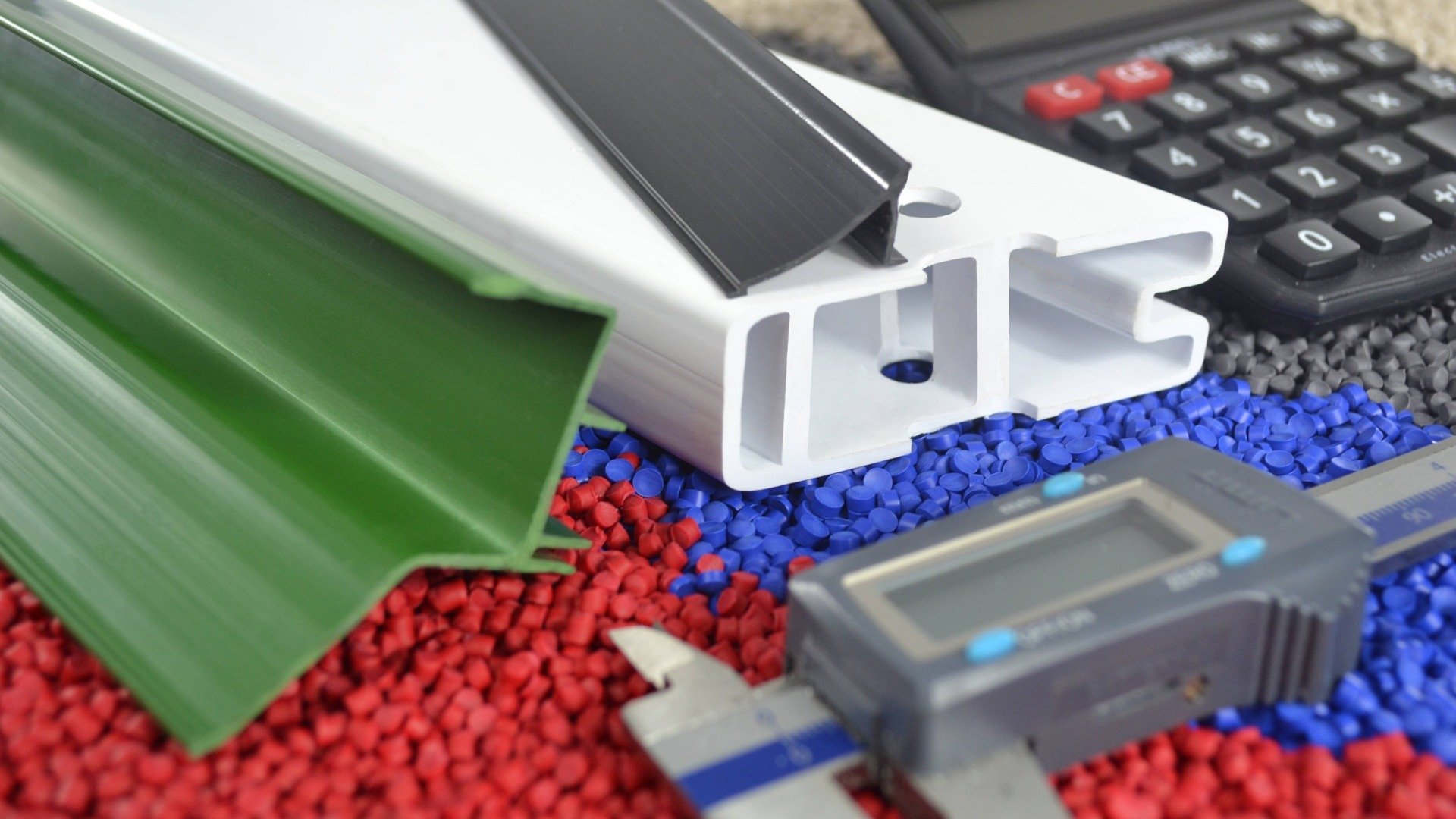
Superior Product Adaptability
Beyond the cost-effectiveness of plastic extrusion, one more substantial advantage in producing lies in its superior item flexibility. This makes plastic extrusion a perfect option for markets that call for personalized plastic parts, such as auto, building and construction, and packaging. In essence, plastic extrusion's product flexibility cultivates innovation while enhancing functional performance.
Improved Production Speed
A considerable advantage of plastic extrusion lies in its boosted production speed. Couple of other production processes can match the rate of plastic extrusion. Additionally, the capability to keep consistent high-speed production without giving up item quality sets plastic extrusion apart from various other approaches.
Real-world Applications and Impacts of Plastic Extrusion
In the realm of manufacturing, the method of plastic extrusion holds extensive importance. This process is extensively made use of in the production of a selection of items, such as plastic tubing, home window structures, and weather stripping. Consequently, it significantly affects industries like building and construction, product packaging, and auto markets. Its impact extends to everyday items, from plastic bags to toothbrushes and non reusable flatware. The financial benefit of plastic extrusion, largely its high-volume and affordable output, has revolutionized manufacturing. The ecological impact of plastic waste stays a worry. For that reason, the industry is constantly pursuing technologies in eco-friendly and recyclable products, indicating a future where the advantages of plastic extrusion can be preserved without jeopardizing environmental sustainability.
Final thought
To conclude, plastic extrusion is a extremely reliable and reliable technique of changing raw materials into varied items. It offers various benefits over various other plastic creating approaches, including cost-effectiveness, high outcome, very little waste, and layout flexibility. Its effect is greatly really felt in numerous industries such as building, vehicle, and customer goods, making it a crucial process in today's manufacturing landscape.
Digging deeper right into the technical process of plastic extrusion, it starts with the selection of the ideal plastic material. When cooled, the plastic is cut into the needed lengths or injury onto reels if the product is a plastic movie or sheet - plastic extrusion. Comparing Plastic Extrusion to Various Other Plastic Forming Methods
Understanding the kinds of plastic ideal for extrusion paves the means for a more comprehensive conversation on just how plastic extrusion piles you can find out more up against other plastic forming methods. Few various other production procedures can match the rate of plastic extrusion.
Report this page